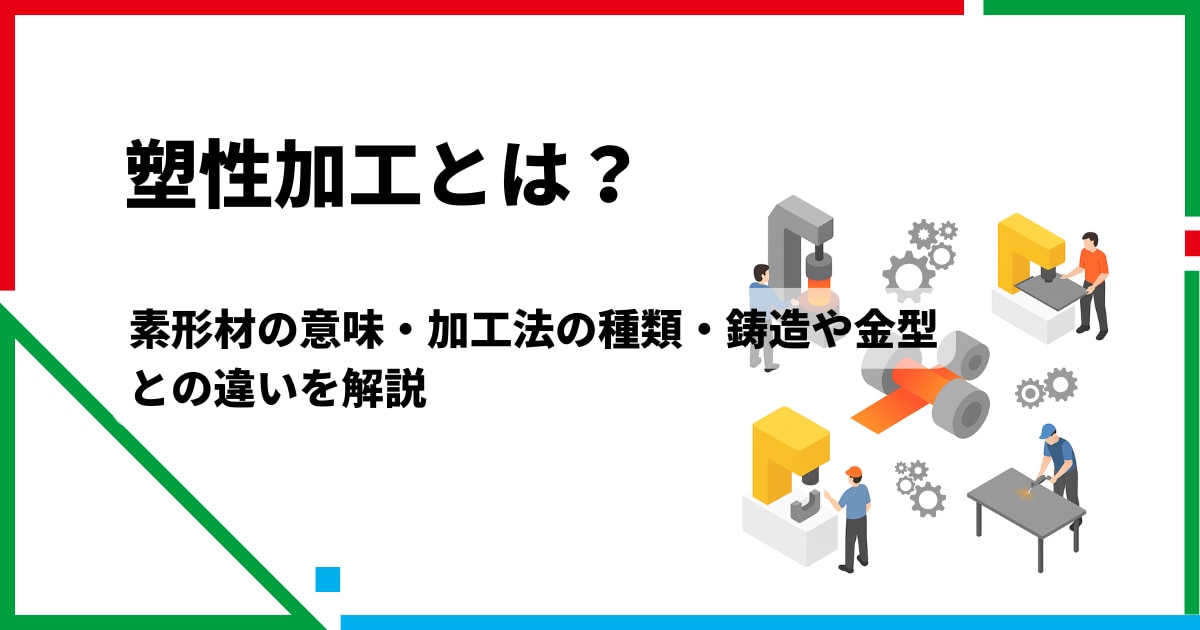
塑性加工とは?素形材の意味・加工法の種類・鋳造や金型との違いを解説
ものづくりにおいて、部品の品質やコストを左右する重要な技術の一つが「塑性加工」です。そして、その塑性加工と密接に関わるのが「素形材」という存在です。
- 部品の品質やコストに課題がある
- もっと効率的な加工方法はないか
- もっと効率的な製造プロセスを模索している
製造業の現場で日々ものづくりと向き合う中で、そんなお悩みをお持ちではないでしょうか?
製造の根幹を支える「塑性加工」と「素形材」に焦点を当て、その基礎から複雑な加工法の種類、さらに混同されやすい鋳造や金型との違いまで、初心者の方にも分かりやすく解説します。
この記事の目次[非表示]
塑性加工とは?
塑性加工とは、金属などの材料に力を加えることで、その材料が持つ塑性(力を加えて変形させると、元の形に戻らず、その変形した形を保つ性質)を利用し、目的の形状に成形する加工技術の総称です。
切削加工のように材料を削り取って形を作るのではなく、「押しつぶす」「引き伸ばす」「曲げる」といった方法で材料を成形します。
塑性加工には、材料のロスが少ない、加工によって材料の強度や靭性が向上するといった、多くのメリットがあります。
主な塑性加工には、鍛造、圧延、プレス加工、板金加工、押し出し、引き抜きなどがあります。
塑性加工の主な特徴とメリット
塑性加工には、他の加工法にはない優れた特徴とメリットがあります。
優れた材料効率とコスト削減
材料を削り出す切削加工と異なり、材料を「変形」させるため、スクラップの発生が少なく、材料の歩留まりが良い加工法です。原材料費の削減に直結し、コスト削減や環境負荷低減にも繋がるというメリットがあります。
材質の強度・靭性の向上と高機能化
塑性加工により、金属内部の結晶粒が微細化したり、内部の気泡や空隙が潰れたりすることで、材料自体が硬くなる「加工硬化」が発生し、強度・靭性の向上といった材質的な改善効果が得られることがあります。
これにより製品の耐久性や信頼性を高めることができます。
大量生産における高い生産性と品質
金型や専用の設備を一度構築すれば、同じ形状の製品を高速かつ効率的に、安定した品質で大量に生産することが可能です。
自動車部品や家電製品など、均一な品質が求められる工業製品の量産に不可欠な技術です。
複雑な形状の一体成形と設計の自由度
材料を流動させる特性を活かすことで、切削加工では難しい複雑な形状や、中空構造を持つ部品を一体成形できる場合があります。
部品点数の削減や軽量化にもつながり、製品設計の自由度が高められるという点も塑性加工のメリットです。
塑性加工のデメリット
塑性加工はメリットが多い一方で、以下のようなデメリットもあります。
高コストと少量生産には不向き
プレス成形や鍛造などでは、製品ごとに専用の金型や大型設備が必要となり、初期投資や維持コストが高額です。そのため少量生産ではコスト回収が難しく、量産向きの加工法と言えます。
加工ひずみと寸法精度の課題
加工中に金属内部に残留応力(加工ひずみ)が生じることがあり、後工程や使用時に歪み、割れ、反りの原因となることがあります。
また塑性変形では、「ばね戻り」などの予測しづらい現象が発生するため、精密な寸法制御には追加の加工(切削や研磨)が必要になる場合があります。
複雑形状の加工と材料変質のリスク
塑性加工は、基本的に材料を押しつぶしたり引き延ばしたりする単純な変形に適しており、複雑な形状やアンダーカットのような構造の加工は難しいです 。
加工硬化によって強度は向上するものの、場合によっては延性や靭性が低下することがあり、後工程での溶接や曲げ加工時にトラブルを引き起こす可能性があります。
工程管理が複雑、製品の再現性の低下
塑性加工は次に記載しているように、加工する材料の温度によって分類されます。
温間・熱間加工を行う場合、厳密な温度管理や酸化対策が必要となり、工程管理が複雑になりやすいです。
また素材のロットや硬さ、加工条件のわずかな違いによって成形結果にバラつきが生じ、製品の再現性が低くなることがある点もデメリットとして挙げられます。
加工温度による分類
塑性加工は、加工する材料の温度によって大きく以下の3つに分類されます。
冷間塑性加工
常温で加工する方法です。
加熱による材料の酸化や変質が少なく、寸法精度や表面の光沢が必要な部品に適しています。加工硬化が顕著に現れ、強度向上が期待できます。
熱間塑性加工
材料を高温に加熱して加工する方法です。
金属が柔軟になり、大きな変形が容易になります。硬度の高い材料や、複雑な形状の成形に適していますが、材料の酸化や寸法変化に注意が必要です。加工硬化が起こりにくいため、その後の加工がしやすいという特徴もあります。
温間塑性加工
冷間塑性加工と熱間塑性加工の中間の温度で行う加工です。
冷間と熱間のメリットを組み合わせたもので、冷間よりも大きな変形が可能で、熱間よりも寸法精度や表面状態を保ちやすいという特徴があります。
素形材とは?塑性加工との関係
素形材は塑性加工と密接に関わり、社会の様々な製品の基盤を支える、日本のものづくりにおける「根幹」をなす存在です。
日本の産業において、素形材産業は『基盤産業』として位置づけられており、その競争力を支えているのは、塑性加工や切削加工といった高度な加工技術です。
経済産業省も素形材産業を日本の製造業の競争力維持・強化に不可欠なものとして位置づけ、その振興に取り組んでいます。
素形材の定義と役割
素形材とは、最終製品の「素」となる「形」を持つ材料の総称です。
具体的には、金属などを加工して作られる、まだ最終製品ではないけれど、製品の形を構成する「もと」となる部品や部材を指します。これらの素形材は、さらに切削加工や組立加工などの後工程を経て、最終的な製品の完成となります。
素形材産業は、自動車だけでなく、航空機、建設機械、家電製品、医療機器、さらにはロボットや半導体製造装置など、ほとんど全ての製造業の最終製品に不可欠な部品の「もと」を供給する、まさに「産業の米」と呼べる基盤産業です。
(素形材産業は、素材メーカーと最終製品メーカーをつなぐ、日本のものづくりの基盤です。
経済産業省 素形材産業ビジョン策定委員会による「素形材産業ビジョン 参考資料集(令和7年3月)」を参考に作成)
もし日本の素形材産業が弱体化すれば、他の組立産業も部品の調達に支障をきたし、国内のものづくり全体が立ち行かなくなる可能性があります。
主な素形材の種類
主な素形材の種類には、以下のようなものがあります。
鋳造(ちゅうぞう)品(鋳物) |
金属を溶かして型に流し込み、固めることで作る |
鍛造(たんぞう)品 |
金属を叩いたり、プレスしたりして成形 |
ダイカスト品 |
金属を溶かして金型に高圧で注入し、精密な製品を成形 |
粉末冶金製品 |
金属粉末を固めて焼結することで作る |
金属プレス品 |
金属板をプレス加工によって成形 |
素形材と塑性加工の密接な関係性
経済産業省 素形材産業ビジョン策定委員会による「素形材産業ビジョン 参考資料集(令和7年3月)」によると、日本の素形材産業の主要需要先は自動車であり、その依存度は更に高まっています。
例えば、自動車の車体軽量化と衝突安全性向上のために使われる高張力鋼板(ハイテン材)は、鉄鋼メーカーが製造する素形材です。このハイテン材を、部品メーカーがホットスタンピングという高度な塑性加工技術で成形することで、薄くて強いボディ部品が製造されます。
このように、素形材と塑性加工は一体となって進化し、産業を支えているのです。
塑性加工は多くの素形材の製造プロセスそのもの
素形材の代表格である鍛造品は、塑性加工の一つである鍛造によって作られます。
プレス加工や板金加工の材料となる金属板は、圧延という塑性加工によって製造された素形材です。パイプや棒材の素形材も、押し出しや引き抜きといった塑性加工によって作られます。
このように素形材そのものの製造プロセスにおいて、塑性加工が不可欠な場合が多くあります。
塑性加工は素形材にさらなる価値を付加する
鋳造品や鍛造品などの素形材は、そのまま最終製品になることもありますが、多くの場合は、さらに塑性加工(例えば、プレス加工で穴を開けたり、曲げたり、絞ったりする等)や切削加工などの後工程を経て、より複雑な形状や高い精度を持つ部品へと加工されます。
塑性加工によって素形材の強度や靭性を向上させる(例:鍛造による組織の微細化)といった、材質的な改善や補強が行われるなど、素形材にさらなる価値を付加しています。
塑性加工の代表的な加工法
代表的な塑性加工技術には、以下のようなものがあります。
鍛造(たんぞう)
素形材の「鍛造品」を直接作る加工法です。
材料を加熱または常温で、ハンマーで叩いたりプレスで押し潰したりして成形します。金属内部の組織が緻密になり、強度や粘り強さ(靭性)が向上するという特徴があります。
自動車のエンジン部品(クランクシャフト、コネクティングロッド)、航空機部品、工具、ボルト・ナットなど、高い強度や信頼性が求められる部品に用いられます。
圧延
ロールと呼ばれる回転する工具の間に材料を通し、圧縮しながら引き伸ばして板や棒状に成形する加工法です。金属板、鋼材やアルミニウム板、銅板などの基本的な素形材の製造に広く用いられます。
大量生産が可能で、均一な厚みや形状の材料を効率的に生産できます。
プレス加工
金型を用いて、金属板に強力な圧力を加え、金型の形状を材料に転写して成形する加工方法です。自動車のボディパネル、家電製品の筐体、電子部品のコネクタ、日用品など、幅広い分野で大量生産に用いられます。
主な加工内容として、
- せん断加工(抜き加工):材料を目的の形状に切断する
- 曲げ加工:材料を特定の角度に曲げる
- 絞り加工:平らな板材料を金型で押し込み、深さのある立体的な形状(カップ状など)に成形する
などがあります。
押出し(押し出し加工)
材料(ビレット)をダイスと呼ばれる穴の開いた型に押し込み、その穴の形状に合わせて長い断面形状の製品(例:アルミサッシ、パイプ)を連続的に成形する加工です。
引抜き(引き抜き加工)
材料(線材、棒材、管材など)をダイスと呼ばれる穴に通し、引っ張ることで、細くしたり、特定の断面形状にしたりする加工です。電線、針金、精密な棒材などの製造に用いられます。
板金加工
薄い板状の金属に力を加えて変形させ、立体的な形状を作り出す加工技術の総称です。主に「手板金」と「機械板金」に大別されます。プレス加工と異なり、必ずしも専用の金型を使用せず、汎用的な工具や機械で多様な形状に対応できる点が特徴です。建築部材、厨房機器、ダクト、ケース、カバーなど、多種多様な製品に適用されます。
主な加工内容として、
- 切断加工:レーザー加工機やシャーリングマシンなどを用いて、金属板を所定の形状や寸法に切り抜いたり、分割したりする
- 曲げ加工:ベンディングマシン(プレスブレーキ)などを用いて、金属板を任意の角度に折り曲げる
- 穴あけ加工:タレットパンチプレスやドリルなどを用いて、金属板に穴を開ける
- 絞り加工:プレス加工の絞り加工と同様に、平らな板材料を型に押し込み、深さのある立体的な形状に成形。板金加工においては、汎用金型や多段加工で対応する場合を指すこともある
などがあります。
試作や小ロット生産、あるいは大型で複雑な形状の部品製造に適している点が特徴です。
塑性加工を支える最新技術動向
日本は長らく「ものづくり大国」として、高い塑性加工技術を培ってきました。特に自動車、家電、精密機器などの産業において、その技術は世界をリードしてきました。
かつては塑性加工で使われる金型の生産額でも世界1位を誇っていましたが、2000年以降、自動車や電機メーカーの海外移転や新興国の台頭により、生産額は減少傾向にあります。特にプラスチック金型などの非金属用の型種で顕著です。
日本の塑性加工業界は、長年培ってきた精密加工技術や熟練技能を持つ多くの中小企業に支えられています。一方でこれらの企業がデジタル化やグローバル化の波に乗れるかどうかが、今後の日本の製造業において競争力を左右する重要な要素となります。
また日本企業は高品質・高精度な製品を武器にしていますが、価格競争が激しい市場では、日本の高コスト構造が弱みとなっている側面もあるのです。
私たちは、長年の経験と実績を持つ機械商社として、お客様の課題解決に最適な塑性加工機械や周辺設備のご提案だけでなく、デジタル化支援、そして高度な加工技術に関するコンサルティングを提供しています。
貴社の製造プロセスに合わせた効率的な製造方法の模索、コスト削減、品質向上など、まずはお気軽にご相談ください。
高強度材・難加工材の加工技術進化
ホットスタンピング(熱間プレス)
自動車の車体軽量化と衝突安全性向上のため、超高張力鋼板(ハイテン材)を高温で加熱・成形し、急冷して強度を出す技術。
日本の自動車産業が強く、そのサプライヤーもこの技術を高度化させています。より複雑な形状や複数の部品を一体成形する技術が進化しています。
難加工材(アルミ、マグネシウム、チタン、CFRPなど)への対応
航空機、医療機器、次世代自動車向けに、難加工材の成形技術(例:温間プレス、超塑性成形、摩擦攪拌接合を応用した成形)が開発・実用化されています。特に航空機分野で日本が遅れているとされるチタン合金やニッケル基超合金の加工技術は、各国で研究が進んでいます。
異種材料接合技術
異なる金属やCFRP(炭素繊維強化プラスチック)を組み合わせて軽量化を図るニーズが高まっており、塑性加工と組み合わせた機械的接合(リベット、クリンチングなど)や、摩擦攪拌接合(FSW)などの技術が進化しています。
デジタル技術の活用(DX化)
CAE(Computer Aided Engineering)によるシミュレーションの高度化
プレス成形解析、鍛造解析、金型寿命予測など、製造前にコンピュータ上で加工プロセスを詳細にシミュレーションし、試作回数の削減、開発期間の短縮、品質向上、不良率低減を図ります。AIを活用した最適化や異常検知も進んでいます。
IoTによる生産現場の可視化・最適化
プレス機械や金型にセンサーを取り付け、圧力、温度、振動などのデータをリアルタイムで収集。設備の稼働状況、部品の生産状況、品質異常の検知、予知保全などに活用し、生産効率と品質を向上させます。
2025年7月16日(水)から開催されたMF-TOKYO2025にて、FSW(摩擦攪拌接合)時の温度・力をモニタリングする技術のデモを実機で行いました。
AIを活用した品質管理・不良解析
熟練者の知見をAIに学習させ、画像認識で不良品を自動判別したり、生産データから不良発生の原因を特定したりする取り組みが進んでいます。
デジタルツイン
物理的な工場や機械をデジタル空間上に再現し、シミュレーションやデータ分析を通じて、リアルタイムで生産プロセスを最適化・制御します。
アディティブ・マニュファクチャリング(AM/3Dプリンティング)との融合
複雑形状部品の製造
従来の切削や塑性加工では困難だった複雑な内部構造を持つ部品(軽量化された航空機部品など)を、金属3Dプリンターで製造する技術が進化しています。
金型製造への応用
冷却水路を最適化した金型(コンフォーマルクーリング)を3Dプリンターで製造し、成形サイクルタイムの短縮や品質向上を図る動きがあります。
ハイブリッド製造
AMで製造した部品を後工程で塑性加工(プレス、鍛造など)で最終仕上げを行うなど、両技術の利点を組み合わせる研究も進んでいます。
加工の自動化・ロボット化
プレス機械への材料供給、加工品の取り出し、金型の自動交換など、搬送工程や周辺作業のロボット化・自動化が進んでいます。これにより、生産効率向上、人手不足解消、安全性確保が図られます。
多品種少量生産に対応するため、段取り時間の短縮や自動化された金型交換システムが重要になっています。
塑性加工と鋳造・金型の違い
塑性加工と混同されやすい言葉に「鋳造」や「金型」があります。それぞれの違いを明確にすることで、最適な加工方法の選定に役立ちます。
塑性加工と鋳造の違い
鋳造(ちゅうぞう)は鍛造(たんぞう)と字が似ているため、よく混同されるのですが、鍛造は力を加えて加工する塑性加工のひとつ、鋳造は材料を溶かして成形する、という違いがあります。
項目 |
塑性加工 |
鋳造 |
加工方法 |
材料を溶かさずに、力を加えて変形させる |
材料を溶かし、型に流し込み、固めて成形 |
材料状態 |
固体(または半固体) |
液体(溶融金属) |
材料ロス |
少ない(スクラップが少ない) |
少ない(湯口・湯道の切断は発生) |
材質変化 |
加工硬化などにより強度向上する場合あり |
冷却速度により結晶構造が変化 |
得意分野 |
板物、棒材、高強度部品の量産 |
複雑な形状、大型部品、多品種少量生産 |
鋳造は材料を溶かすのに対し、塑性加工は溶かさないのが大きな違いです。鋳造は複雑な形状を一体で作りやすいですが、塑性加工(特に鍛造や圧延)は材料の組織を緻密にし、強度を高める点で優位性があります。
塑性加工と金型の関係性
項目 |
塑性加工 |
金型 |
役割 |
材料を形にする「加工技術」の総称 |
塑性加工(特にプレス加工)で使う「道具」 |
独立性 |
加工そのもの |
単体では機能せず、機械と組み合わせて使う |
目的 |
部品の製造 |
特定の形状を材料に転写するためのツール |
金型は、プレス加工や鍛造、ダイカストといった塑性加工において、材料を目的の形状に成形するための「型」や「工具」です。金型が高精度であればあるほど、生産される部品の精度や品質も高まります。
つまり、金型は塑性加工を効率的かつ高精度に行うための重要なツールであり、両者は切っても切れない関係にあります。
まとめ
塑性加工と素形材は、現代のものづくり、特に自動車や航空機、家電といった産業の根幹を支える不可欠な技術と産業です。塑性加工は材料の特性を最大限に引き出し、高精度かつ高効率な部品製造を可能にします。そして、その塑性加工によって生み出される「素形材」は、あらゆる最終製品の品質と性能を決定づける重要な出発点となります。
近年では、自動車の軽量化・高強度化のためのホットスタンピング技術の進化や、CAEシミュレーション、IoTによる生産現場の可視化、AIを活用した品質管理といったデジタル技術(DX)の活用が急速に進んでいます。
また、3Dプリンターが金型製造や試作に活用されるなど、異分野の技術との融合も進んでおり、塑性加工は今後もさらなる技術進化への期待が高まっています。
材料の特性を最大限に引き出し、より高機能で環境負荷の低い製品を生み出す塑性加工には、これからも期待が膨らむ分野です。
私たちは、長年の経験と実績を持つ機械商社として、お客様の課題解決に最適な塑性加工機械や周辺設備のご提案、デジタル化支援、そして高度な加工技術に関するコンサルティングを提供しています。
貴社の製造プロセスに合わせた効率的な製造方法の模索、コスト削減、品質向上など、まずはお気軽にご相談ください。