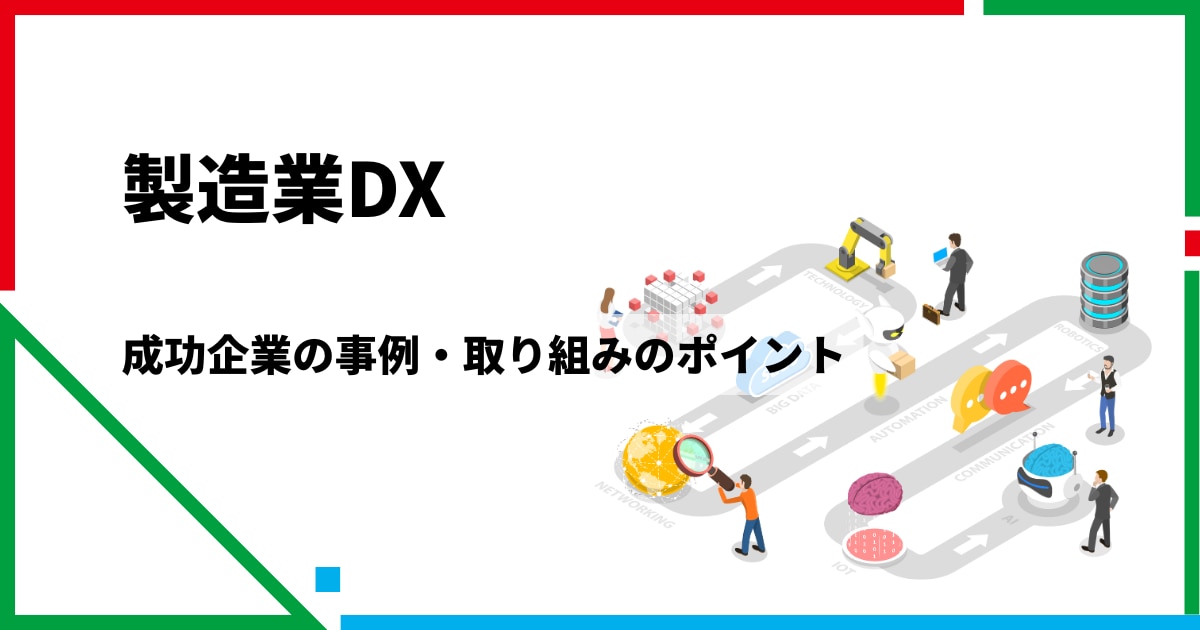
製造業DXの事例を徹底解説 | 成功企業に学ぶ取り組みのポイントとは?
そもそも「製造業DX」とは?
製造業においては、属人化された作業や紙ベースの業務が残る現場も多く、業務の非効率さが利益圧迫要因となっています。こうした環境下で、ITやデータを活用して「業務効率の改善」「品質の安定」「経営判断の迅速化」などを実現し、従来の業務プロセスやビジネスモデルを根本から変革する手段として、DX(デジタルトランスフォーメーション)が注目されています。
製造業においては、工場や生産現場におけるリアルタイムな可視化、省人化、予防保全の仕組みづくりなどが主な対象になります。
この記事の目次[非表示]
なぜ今、製造業にDXが必要なのか?
製造業DXと言われる背景には、日本の製造業が抱える以下のような構造的課題があります。
労働力不足・熟練技能の継承困難
少子高齢化の進行により、製造現場では若年層の担い手が減少し続けています。その一方で、ベテラン人材に蓄積された技能やノウハウが属人化しており、体系的な継承が難しい状況が各地で生じています。
こうした課題に対応するため、製造業ではAIによる外観検査やAGVによる物流自動化、RPAやデジタル工作機械の活用など、省人化を前提とした生産体制の構築が進んでいるのです。
人手不足の解消と同時に、熟練技能をデジタル技術で「見える化」し、誰でも再現可能な状態にすることが求められています。
グローバル競争激化とQCD要求の多様化
グローバル競争が激化する中、製造業には価格、品質、納期の3要素(QCD)だけでなく、それらを同時に高水準で満たすことが求められています。さらに、顧客ごとのカスタマイズ対応やスピード納品、環境配慮といった新たな要素も評価対象になっています。
このような変化に対応するためには、工場内の設備や人の動きをIoTやクラウド型MESで可視化・統合管理する「スマートファクトリー」のような仕組みが有効です。生産の遅延や不良の兆候をリアルタイムで把握し、柔軟に調整できる体制をつくることで、QCDの基準や求められる内容が多様化する中でも、透明性と即応性を備えたプロセスが実現できます。
デジタルの活用なくして、スピードと不確実性を伴う現在の変化の中で、持続的に競争力を保つことは難しくなってきています。
ESG・カーボンニュートラルへの対応
環境や社会、企業統治に関する責任を果たす「ESG(環境・社会・ガバナンス)」の視点は、今や製造業にとっても不可欠な経営課題です。特にカーボンニュートラル(温室効果ガス排出の実質ゼロ)への対応は、国内外の取引先や投資家からも強く求められています。
社会的要請・社会的責任に応えるためには、工場のエネルギー消費量やCO₂排出量の可視化、設備稼働の最適化が必要です。IoTセンサーやEMS(エネルギーマネジメントシステム)の導入により、環境負荷の低減と生産性向上の両立が図られています。
製造業は複合的な課題に直面しています。
製造業がDXを進めることは、単なる業務効率化ではなく、未来の競争力を確保するための経営戦略そのもの、と言えるのです。
製造業DXの最新事例9選
製造業DXは、業界・企業規模を問わず加速しています。いずれも単なるIT導入ではなく、事業変革・顧客価値の向上につながっている事例をピックアップしました。
1.トヨタ自動車株式会社|マテリアルズ・インフォマティクス(MI)による材料開発DX
材料開発にマテリアルズ・インフォマティクス(MI)を導入して、AIとビッグデータを活用しています。膨大な素材配合や特性データをもとに新材料の設計を高速化しました。従来、試作と評価を何度も繰り返していた工程を、データ解析により事前に最適候補を絞り込めるようになったことで、開発期間を大幅に短縮。
新製品投入のスピードと競争力を両立し、試作コストの削減にもつながっています。
参考)https://www.mi-seek.com/success-stories/toyota-success-story.html
2.パナソニックホールディングス株式会社|モーター設計にAI活用
電動シェーバーに搭載するモーターの設計業務にAI技術を導入。 過去の試作データとCAE解析結果を学習させたことで、設計検討の期間が大幅に短縮されました。 AIの活用により、熟練設計者のノウハウを組織知として活用できるようになり、開発コストの削減と品質の標準化を同時に実現しています。 参考)https://xtech.nikkei.com/atcl/nxt/column/18/00001/07922/
3.旭鉄工株式会社/i Smart Technologies株式会社|IoTで生産性向上+ノウハウの外販
自社工場にIoTセンサーと生産管理システムを導入。 生産状況のリアルタイム監視と分析により、ボトルネック工程の特定と改善を迅速に行えるようになりました。さらに、そこで得た改善ノウハウを外販し、新たな収益モデルも確立しています。製造業からソリューション提供企業へと進化した製造業DX事例です。 参考)https://case-studies.ipa.go.jp/jirei-data/case_studies/102
4.某自動車部品メーカー|設備保全・予防保全の効率化
切削加工において重要な役割を果たすクーラント(切削液)。適切なクーラント管理は工具寿命の延長、加工精度の向上、設備の保護を行います。
毎日行っていたクーラント管理を自動化することにより、生産性と品質が向上しただけでなく、点検作業に費やしていた時間を他の重要な業務に振り向けることが実現できています。
参考)
5.株式会社山本金属製作所 | IoT×工具寿命×熟練技術の可視化
機械加工事業や、ソリューション事業、ロボット SIer 事業、技術教育支援事業の 4 部門を展開する同社は、切削加工における工具摩耗をIoTセンサーで可視化。熟練工の経験則を数値化し、技能伝承と生産性の両立を図っています。また異常検知も自動化し、予防保全にもデータ活用しています。
参考)https://www.ipa.go.jp/digital/dx/mfg-dx/ug65p90000001kqv-att/000109368.pdf
6.株式会社旭ウエルテック | 職人技の“虎の巻”をタッチパネルで見える化
多品種少量生産の現場で、職人の技術やノウハウの継承が課題であった同社は、職人のノウハウをデジタルで見える化しました。「虎の巻」データを作成し、大型タッチパネルで表示することで誰でも熟練者と同様の作業が可能になり、技術継承を効率化したDX事例です。
参考)https://case-studies.ipa.go.jp/jirei-data/case_studies/100
7.日本ツクリダス株式会社 | 町工場から“ものづくりサービス企業”へ
金属加工の町工場から「ものづくりサービス企業」へと進化した事例です。「ものづくり」と「ことづくり」の2つの事業を柱とし、「ことづくり」事業において、属人化した業務の仕組みを見直し、デジタル化ツールを活用して業務を効率化しました。「ことづくり」事業においてそのノウハウをもとに、独自の生産管理システムを開発・販売。HPや名刺制作なども行い、製造×デザインの新業態を展開しています。
参考)https://case-studies.ipa.go.jp/jirei-data/case_studies/103
8.株式会社樋口製作所 | スマートファクトリー実現を目指すDX推進
同社は金属プレス専門メーカーとして、スマートファクトリー実現を目指しDXを推進しています。データ共有基盤に加え、設備自律化(Check Master)、技術伝承AI(Hawk AI)、管理者AI(Lai-ser)など多様なシステムを自社開発・活用。これにより、年間8100時間の労働時間削減や一人当たり生産性向上、不具合の大幅削減を実現。
経営者のリーダーシップと、現場を巻き込んだアジャイル開発が成功要因と書かれています。
9.某機械製造業|クラウド活用で営業効率・成約率向上
クラウドサービス「ゲンバト - 製造現場にちょうどいいデジタルを -」の「エンムスビ」を活用。
得意な製造・加工を持つ会社と製造・加工を依頼したい会社をマッチングするクラウドサービスを利用。人手不足で新規取引先獲得に手が回らず、閑散期には稼働していない期間があるなど課題が解決し、自社でDX構築を考えるのではなく外部サービスを活用することも製造業DXの一手と考えています。
参考)
経産省資料から見る製造DXの失敗・停滞つまづきポイント3選
経済産業省が2024年5月に公開した資料「製造業を巡る現状と課題 今後の政策の方向性」は、公開当時SNSで話題になりました。
この資料では、製造業DXは、単なるデジタル技術の導入に留まらず、グローバル化や市場変化に対応するための経営モデル、組織構造、人材育成、意思決定スタイルといった日本的経営の根源的な課題を克服し、全体最適を目指すための変革であることを強調しています。
経産省資料から、製造業DXでの失敗や停滞を生んでしまったつまづきポイントについてまとめます。
Case1. レガシー設備との接続でコスト超過
多くの製造業では、長年使用されてきたレガシー設備が現場に存在しています。これらの設備は、最新のデジタル技術との互換性が低く、接続やデータ取得が困難です。
そのため、DXを進める際に、既存設備との接続やデータ連携に予想以上のコストが発生し、プロジェクト全体の予算を圧迫するケースがあります。
例えば、ある企業では、既存の生産設備と新たに導入するIoTシステムとの接続に多額の費用がかかり、当初の予算を大幅に超過しました。
このような事態を防ぐためには、事前に設備の現状を把握し、必要な改修や投資を見積もることが重要です。
Case2. 現場巻き込み不足でPoC止まりで実装に至らず
DX推進において、現場の理解と協力は不可欠です。
しかし、経営層やIT部門が主導で進めた結果、現場の意見やニーズが反映されず、PoC(概念実証)段階で止まってしまうケースがあります。現場の業務フローや課題を十分に理解せずに進めた結果、導入されたシステムが実際の業務に適合せず、現場からの反発を招くこともあります。
成功するためには、現場の意見を取り入れた上で、段階的に導入を進め、効果を実感してもらうことが重要です。また、現場担当者への教育やサポート体制の整備も欠かせません。
Case3. セキュリティ要件未整備で全社展開が遅れた
クラウドサービスの活用などDXを進めることにより、製造業のシステムは外部との接続が増え、サイバーセキュリティのリスクも高まります。しかし、セキュリティ対策が不十分なままシステムを導入した結果、セキュリティインシデントが発生し、全社展開が遅れるケースがあります。
例えば、ある企業では、工場のネットワークがサイバー攻撃を受け、生産ラインが停止する事態に陥りました。
このようなリスクを回避するためには、システム導入前にセキュリティ要件を明確にし、適切な対策を講じることが必要です。また、定期的なセキュリティ教育や訓練も重要になります。
製造業DXの失敗に陥りやすいポイントと回避法
製造業DXを進める企業は年々増加しているのですが、「期待したほど効果が出ない」「現場が動かない」という声は後を絶ちません。
経済産業省の調査によれば、日本企業のDX推進の事例のうち、約9割が個別のオペレーションや現場改善にとどまり、経営全体を変革するような「全社的DX」に取り組めているのは1割に過ぎないそうです。
このような背景をふまえ、特に製造業に多い失敗に陥りやすいポイントをいくつか紹介しつつ、実践的な回避策を解説します。
1.個別最適で満足し、全体最適に至らない
ある工程でIoTを入れて効果が出たからといって、それが企業全体の生産性向上や利益創出につながるとは限りません。特定部門や工場だけで成果が止まり、サプライチェーン全体の変革や経営インパクトにはつながらないケースが多く見られます。
これを避けるためには、DXを「経営課題」と位置づけ、最初から全社視点で設計図を描くことが重要です。
2.現場と経営が分断されている
経営層がビジョンを描いても、現場が「やらされ感」で動いていると、PoC(概念実証)で止まり、本番導入に至りません。逆に現場主導で進めたDXも、経営判断の支援がなければ全社展開は難しくなります。
部門間の壁を超え、経営と現場が対話しながら進める体制づくりが鍵となります。
3.IT人材がいない
日本の製造業、とくに中堅・中小企業では、社内にDXをリードできるIT人材がいないという悩みがよく聞かれます。
ポイントは「内製化」に固執せず、社外やクラウドサービスなど外部の力をうまく借りながら、自社に必要な“役割”を定義することです。
たとえばこのような役割を考えておきます。
- 商社やSIer、産業支援機関と連携して、技術的支援を得る
- 社内に「DX推進担当」を任命し、学びながら旗振り役を担う
- 他社事例を参考に、外部パートナーとの協働モデルを設計する
DXは最初から完全装備で始める必要はありません。
「学びながら進める」「スモールスタートで始める」ことで、自走力を少しずつ高めることができます。
4.投資対効果を考えると自社には不要では?と感じる
製造業DXを進めるうえで、やはり気になるのは投資金額。投資回収ができるのか?といった観点では、短期の成果よりも、中長期的な構造改革の視点が必要になります。
そのためには「何に投資し、何を得るか」を明確にするKPI設計が欠かせません。
投資対効果を考える際は、単にコスト削減だけでなく、売上成長、顧客体験の向上、新たなビジネスモデル創出なども含めて考えましょう。
またDXを進めるうえでのハードルになりがちな初期投資については、補助金を活用している事例も多いです。
- IT導入補助金
- ものづくり補助金(設備投資・システム開発支援)
- 事業再構築補助金(抜本的な事業転換や新市場開拓)
などの補助金が製造業では多く利用されています。
※補助金について詳しくは「補助金情報」にまとめていますのでご覧ください。
\製造業向けの主要な補助金について、分かりやすく比較表にしています/
ダウンロードしてご活用ください。
成功事例から学ぶ、製造業DXを成果につなげるための6つのチェックポイント
製造業のDXは、単なるITツールや技術導入の話ではありません。社内の「やり方」や「役割」そのものを問い直す、言ってみれば「経営の中身を入れ替える作業」です。
実際に全体最適へ踏み出した企業の事例や取り組みから、成功のための共通項が見えてきます。
DXを成果につなげるために意識すべき6つのチェックポイントをまとめました。
ポイント1.目的や課題を明確にする
DX推進の第一歩は、「なぜやるのか」を明確にし、社内で共有することです。「なぜやるのか」が曖昧なままだと、せっかく導入した仕組みも「誰のため?」となってしまい現場で使われないものになってしまいます。
「人材不足解消」「在庫適正化」「納期遅延を改善」「属人化を減らす」など、解決すべき具体的な課題を明確にし、社内で共有することで、何をやるべきかの方向性や優先順位が定まり、現場との共通認識も生まれます。
目的が曖昧なまま進めると、ITツールやシステム・設備導入が目的になってしまい、全体的な効果が見えなくなってしまいます。
たとえば、「人手不足」という課題に対して「人を増やす」「技術スキルを向上させる」というのも解決策です。
一方で「できるだけ自動化できる部分は自動化し、プログラミングで対応できる部分は機械に任せ、省人化できる工作機械のデジタル化を進める」といった解決策も考えられます。
目的や課題を明確化し、社内で共通認識をもつことができれば、DX推進はスムーズに進み、無駄な投資を減らせます。
ポイント2.DX推進は小さな成功から始める「スモールスタート」
いきなり全社展開を目指すのではなく、特定の工場や工程、製品ラインなどでPoC(概念実証)を実施し、短期間で成果を出すことが肝心です。
実際、成功事例の多くは「最初は1ラインだけ」「1業務だけ」から始め、そこから横展開していく進め方をしています。
スモールスタートは部分最適ではありません。目的や課題を明確にして全体最適を見据えているからこそのスモールスタートです。
「まずは○○工場から」「まずはこの工程だけ」と小さく始めて、「効果が出た」という事実を積み重ねていくことで、社内全体の理解が一気に進みます。
ポイント3.経営層・現場の巻き込みと全社的な推進体制
経営層が「DXは経営課題である」と明言し、現場と連携しながら推進する体制が重要です。現場だけに任せるのではなく、経営・IT・製造・営業が一体となって動く「横断的チーム」をつくり、定期的に進捗と効果を確認・修正するサイクルを持つ企業ほど、全体最適へとつながっています。
日々の業務に追われてそんな時間はない、と感じる現場の方は多いです。これが起こりがちなのは、経営層から頭ごなしに言われ「やらされ感」があったり「また上が勝手に決めた」と現場が感じる場合です。
一方で、現場が課題をもって解決したいがためにデジタル化・DX化を推進しようとしても、「投資に見合う回収ができるのか?」と経営層から言われストップしてしまうこともあります。
これは目的や課題が全社で明確化されていないこと、バラバラで動いてしまっていることが原因です。
製造業DXへの取り組みは、全社的な推進体制づくりがとても重要になってきます。
ポイント4.データ活用の仕組みづくり
製造現場では日々大量のデータが生まれていますが、それを「見える化」し、「意味ある情報」に変え、「現場の意思決定」に活かせている企業はまだまだ少ないです。
「記録はあるけど見ていない」「紙はあるけど探せない」こういう企業は多いです。
現場改善のスピードと精度を高め、作業効率をあげるため、IoTセンサーやMES、BIツールなどデータを情報に変え、その情報を活用する仕組みづくりが欠かせません。「勘と経験」で行っていたものづくりから「データに基づくものづくり、データに基づく判断」へと移行できます。
たとえば、「品質管理の高度化・効率化」という課題があったとき、データ分析による不良要因の特定や業務効率化など、データを活用した品質管理を行う、という解決策も考えられます。
詳しくは「【経営者・品質管理者向け】品質管理DXセミナー」のアーカイブ配信をご覧ください。
ポイント5.外部支援サービスの活用方法と選び方
DX推進には、システム・業務・現場の幅広い知見が求められます。全てを内製化するのは現実的でなく、成功している企業は、信頼できる製造業商社やSIer、コンサルティングパートナーと連携し、自社にない知識やリソースを補完しています。
ポイントは「丸投げしないこと」。自社の目的と課題をしっかり伝え、対話を重ねながら進める関係が重要です。
ポイント6.全体最適への視点を忘れない
1つの工場、1つの工程で成果が出ても、それが全社最適につながらなければ、部分最適に留まってしまいます。
製造業DXの多くが「個別最適」で止まってしまう中、全体最適を意識して推進する企業は、業務改善を超えて「収益構造の再構築」や「新たなビジネスモデル創出」につなげています。
点で終わらせず、線や面に広げる視座を持つことが、長期的な競争優位を築く鍵になります。
まずは一歩。スモールスタートから始めることが大事です。
多くの製造業では業務に直結する製造工程をスモールスタートで取り組むことが多いです。
製造業DXで重要なのは「何を変えたいか」を見失わず、社内外の力を借りながら着実に一歩ずつ進めていくことです。
事例でご紹介していますが、「ゲンバト - 製造現場にちょうどいいデジタルを -」は、製造DXスモールスタートに最適なクラウドサービスです。
DX何から始めれば?とお困りでしたら、製造工程におけるデジタル化への取り組みや補助金の活用など、製造業の課題解決において経験豊富な私たちにぜひご相談ください。